1. Yleiskatsaus tuotantoprosessiin
Raaka-aineen valmistus: Tuotannossa käytetyt raaka-aineet Soijamaitopussi CPP/PE-kalvo sisältävät pääasiassa CPP (valettu polypropeeni) ja PE (polyeteeni) hiukkasia. Näille raaka-aineille on suoritettava tiukka seulonta ja laadunvalvonta, jotta varmistetaan raaka-aineiden puhtaus ja vakaus. Sen jälkeen raaka-aineet sekoitetaan ennalta määrätyn kaavasuhteen mukaisesti valmistellakseen myöhempää tuotantoa varten.
Sulapuristus: Sekoitettu raaka-aine syötetään sulaekstruuderiin. Ekstruuderissa raaka-aineet kuumennetaan korkeisiin lämpötiloihin ja sulavat vähitellen viskoosiksi nestemäiseksi. Tämän prosessin aikana parametreja, kuten lämpötilaa, painetta ja nopeutta, on säädettävä tarkasti, jotta varmistetaan raaka-aineiden tasainen sulaminen ja sopivat sulat materiaalit myöhempää muovausta varten.
Kalanterointi: Kun sula materiaali tulee ulos ekstruuderista, se menee kalanteriin muotoilua varten. Kalanteri koostuu useista teloista. Säätämällä telojen välistä rakoa ja painetta sula materiaali kalanteroidaan kalvoksi. Kalanterointiprosessin aikana on tarpeen varmistaa, että kalvolla on tasainen paksuus, sileä pinta ja se täyttää ennalta määrätyt fysikaaliset suorituskykyvaatimukset.
Jäähdytys ja jähmettyminen: Kalanteroitu kalvo on jäähdytettävä ja kiinteytettävä sen rakenteen ja suorituskyvyn vakauttamiseksi. Jäähdytysmenetelmänä voi olla ilmajäähdytys tai vesijäähdytys, joka valitaan tuotantotarpeiden ja tuotteen ominaisuuksien mukaan. Jäähdyttämällä kalvon molekyyliketjut kiinnittyvät, mikä parantaa sen mekaanisia ominaisuuksia ja stabiilisuutta.
Kelaus ja leikkaus: Jäähtymisen ja jähmettymisen jälkeen kalvoa rullataan jatkuvasti suureksi kalvotuotteeksi. Myöhemmin kalvo leikataan tuotteen eritelmien ja kokovaatimusten mukaisesti leikkauskoneella Soijamaitopussi CPP/PE-kalvo joka täyttää vaatimukset.
Laaduntarkastus ja pakkaus: Suorita leikatun kalvon laaduntarkastus, mukaan lukien paksuuden, lujuuden, ulkonäön jne. tarkastus. Kun on varmistettu, että tuote täyttää laatustandardit, se pakataan, merkitään ja valmistetaan lähetettäväksi tehtaalta. Koko tuotantoprosessin ajan tuotantoympäristöä on valvottava tarkasti tuotantopajan puhtauden ja hygienian varmistamiseksi. Samalla vahvistetaan laitteiden huoltoa ja kunnossapitoa tuotantolaitteiden normaalin toiminnan ja vakauden varmistamiseksi.
2. Paksuuden hallinnan merkitys
Paksuus on tärkeä suorituskyvyn parametri Soijamaitopussi CPP/PE-kalvo . Liian ohut kalvo ei ehkä kestä pakkauksen sisällön aiheuttamaa painetta, mikä aiheuttaa repeämisen tai vuotamisen; kun taas liian paksu kalvo aiheuttaa raaka-aineiden hukkaa ja nostaa tuotantokustannuksia. Siksi kohtuullinen paksuuden hallinta on avain tasapainon saavuttamiseen tuotteen lujuuden ja kustannustehokkuuden välillä.
3. Paksuuden hallintastrategia
Raaka-aineiden valinta ja annostelu
Valitse korkealaatuiset CPP- ja PE-hiukkaset ja mittaa ne tuotteen suorituskykyvaatimusten mukaan. CPP- ja PE-hiukkasten erilaiset suhteet vaikuttavat kalvon mekaanisiin ominaisuuksiin ja hintaan. Suhdesuhdetta optimoimalla voidaan alentaa raaka-ainekustannuksia ja samalla varmistaa lujuus.
Sulapuristusprosessin ohjaus
Suulakepuristusprosessin aikana parametreja, kuten lämpötilaa, painetta ja ekstruuderin nopeutta, valvotaan tiukasti sen varmistamiseksi, että sula materiaali virtaa ulos tasaisesti ja vakaasti. Säätämällä ekstruuderin parametreja voidaan saavuttaa tarkka kalvon paksuuden säätö.
Kalanterointiprosessin optimointi
Kalanterointi on avainvaihe kalvon paksuuden säätelyssä. Kalvon paksuuden tarkka säätö voidaan saavuttaa säätämällä parametreja, kuten telaväliä, painetta ja kalanterin nopeutta. Samaan aikaan kalanterointiprosessin optimointi voi myös parantaa kalvon tasaisuutta ja pinnan laatua.
Paksuuden seuranta ja palaute verkossa
Asenna paksuuden valvontalaitteet tuotantolinjalle seurataksesi kalvon paksuuden muutoksia reaaliajassa. Kun paksuus poikkeaa asetetusta arvosta, asiaankuuluvat prosessiparametrit säädetään välittömästi takaisinkytkentäjärjestelmän kautta sen varmistamiseksi, että kalvon paksuus on aina kohtuullisella alueella.
4. Tasapaino kustannusten ja intensiteetin välillä
Paksuuden hallintaprosessissa on otettava huomioon kustannusten ja lujuuden välinen tasapaino. Toisaalta raaka-ainesuhdetta ja prosessiparametreja optimoimalla raaka-aineen kulutusta ja energiankulutusta vähennetään, mikä alentaa tuotantokustannuksia; toisaalta varmistetaan, että kalvon paksuus täyttää pakkausvaatimukset ja vältetään riittämättömän lujuuden aiheuttamat laatuongelmat. Varsinaisessa käytössä kalvon paksuus- ja lujuusvaatimuksia voidaan säätää joustavasti markkinoiden kysynnän ja tuotteen sijainnin mukaan parhaan taloudellisen hyödyn saavuttamiseksi.
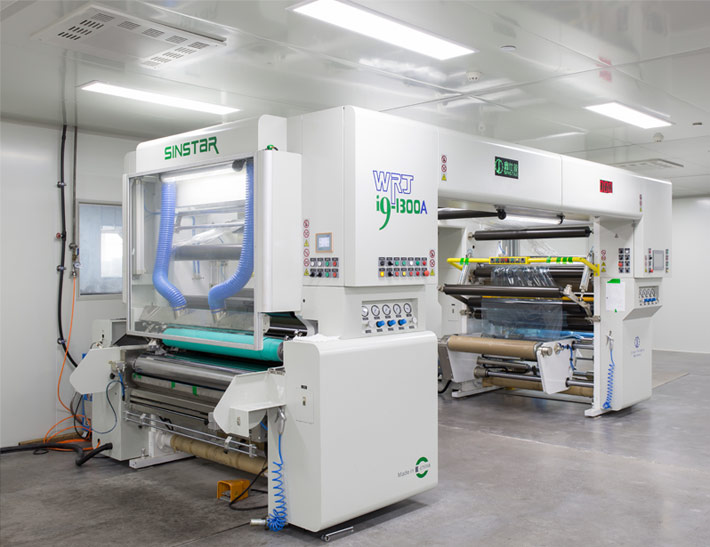